What is “work design” and why does it matter?
The Broad Institute is highly esteemed, famous for pioneering research of the human genome. But increased demand for its genome sequencing service, as well as technology evolving and changing at a great rate, led to day-to-day operations being halted. The organization’s average turnaround time for a DNA sample was 120 days and staff struggled to manage the fifty sequencing machines, which were operating under 50% utilization.
Shift Gear, a company focused on helping organizations refine their processes and work design, stepped in, improving the layout of laboratory operations so that it better suited the staff working in the laboratory; as well as implementing a “pull system” – a control-oriented system that operates by receiving signals that more production is needed.
These improvement strategies reduced turnaround times of samples from an average of 120 days to just 12 days and increased the utilization rates of the machines to more than 85% – allowing the Broad Institute to now process 1 million samples annually.1
The initial issues with the Broad Institute emerged due to static work design – a common problem in most organizations. Static work is the norm – drawing up organizational charts or having the product move systematically from one machine to the next – but what happens when problems arise that are not catered for in the static systems you’ve implemented?
Perhaps communication breaks down, response times increase, orders get delayed, costs rise and everyone is on edge. ShiftGear’s solution to this issue of static work design was to teach the Broad Institute how to proceed from, what they have coined, “Dynamic Work Design”, rather than a statically-designed operational system.
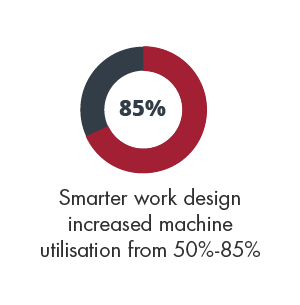
At the core of Dynamic Work Design is the understanding that every pain point is an opportunity for innovation and improvement, and it builds on the foundational idea that unplanned events will happen in an organization, but the way an organization, or more specifically, the leader of an organization, responds to those events is vital to the longevity and success of the business.
You may be wondering why this method of work design is a better approach than process design or organization design. A research paper, written by MIT Sloan School of Management Distinguished Professor of Systems Dynamics and Organizational Studies, Nelson Repenning, explains it well:2
“A critical limitation of both approaches is that neither takes particular account of the fallible human beings who will be doing the jobs that a given design specifies. While process designers do attend to ergonomic issues, they focus largely on human physical limitations and give little attention to the cognitive or emotional dimensions. Similarly, those focused on organization design typically presume both that people will execute their role in the organization chart in the way that the designer intended and that work will typically go as planned…Work design departs from its process and organization-focused brethren by focusing on creating work that matches the skills and capabilities of those who do it. Rather than presuming an “ideal” employee, work design takes the human condition as given and attempts to create work that is consistent with our inherent strengths and limitations.”
Four key principles for implementing smarter work design
Implementing smarter work design and continuous improvement strategies is entrenched in four key principles that were developed by ShiftGear, namely: Align and Reconcile Intent and Activity; Connect the Human Chain Through Triggers and Checks; Structured Problem-Solving and Creativity; and Optimal Challenge.3
Align and Reconcile Intent and Activity
This is about gaining clarity on the mission, goals and objectives of your organization and then ensuring that every work activity – by human and machine – is woven into an integrated system to meet these goals.
Connect the Human Chain
People are the building blocks of any organization, and even the slightest communication breakdown can cause a system to crash. In order to ensure good work design, a system needs to be implemented that enables and encourages teams and managers to check-in with each other frequently, to ensure that problems and concerns can be resolved with immediate effect.
Structured Problem-Solving
Instead of jumping to intuitive solutions when a problem arises, good work design happens when the proper analysis is implemented within a structure, utilizing data and thorough investigation into the root of the problem.
Optimal Challenge
To ensure a system is working to its optimal potential, plug in enough stress to surface any problem areas while setting aside enough time to resolve these problems.
Whether it’s oil, DNA sequencing, or engineering, Dynamic Work Design can be applied across a diverse range of businesses and is key to sustainable improvement, increased productivity and positive employee engagement within an organization.
For example, by encouraging employees to look for new, better ways of doing their jobs, not only will the work be more efficient, but the employee will have a greater sense of ownership and therefore engagement with his/her work.
In the words of Nelson Repenning:
“It’s how organizations respond to the inevitable problems and hiccups that make all the difference in the world. Rather than punishing employees for mistakes (and incentivizing them to hide their shortcomings), firms that take a dynamic approach continuously encourage them to find new and better ways to do their jobs.”4
Do you want to think about your work in a whole new way?
Enroll in the MIT Sloan Business Process Design for Strategic Management online short course today and lead smarter work design in your organization.